In the continuum damage mechanics formalism, a damage variable represents the amount of deterioration due to crack growth. This damage variable controls the weakening of the material’s stiffness, and it produces a nonlinear relation between stress and strain.
For a linear elastic material, Hooke’s law relates the undamaged stress tensor
σun to the elastic strain tensor:
(3-68)
here, C is the fourth order
elasticity tensor, “:” stands for the double-dot tensor product (or double contraction). The elastic strain
εel is the difference between the total strain
ε and inelastic strains
εinel. There may also be an external stress contribution
σex, with contributions from initial, viscoelastic, or other inelastic stresses. For a hyperelastic material, the undamaged stress tensor follows from the definition of the second Piola–Kirchhoff stress in
Hyperelastic Materials.
For the scalar damage models, the damaged stress tensor
σd is computed from the undamaged stress as
(3-69)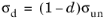
This damaged stress is then used in the weak formulation. There are different ways to compute the scalar damage variable d that controls the material weakening. These are listed in the following sections. When a large strain formulation is used,
σun and
σd should be interpreted as the second Piola–Kirchhoff stress.
The strain-based formulation for the Scalar damage and the
Mazars damage for concrete models is based on the loading function
f such as
(3-70)
here, εeq is the equivalent strain, a scalar measure of the elastic strain; and
κ is a state variable. The evolution of the state variable
κ follows the Kuhn–Tucker loading/unloading conditions
In this formulation, κ is the maximum value of
εeq in the load history. The damage variable
d is then computed as a function of the state variable
κ and other parameters.
Different damage models use different definitions for the equivalent strain εeq. The
Rankine, stress damage model defines the equivalent strain from the largest undamaged principal stress
σp1 as
(3-71)
Here, “<·>” represent the Macaulay brackets and E is Young’s modulus. The Macaulay brackets are used since in this formulation only tensile (positive) stresses cause damage.
Similarly, the Rankine, strain damage model defines the equivalent strain from the largest principal elastic strain
εelp1 as
(3-72)
The Smooth Rankine, stress damage model defines the equivalent strain from the three undamaged principal stresses
(3-73)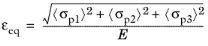
In the same way, the Smooth Rankine, strain damage model defines the equivalent strain from the three elastic principal strains
(3-74)
The Euclidean Norm of the elastic strain tensor can also be used as a measure for the equivalent strain
(3-75)
For the Mazars damage for concrete model, it is also possible to select from
Mazars or
Modified Mazars equivalent strain. Mazars equivalent strain is defined as
(3-76)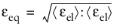
In the modified Mazars equivalent strain (Ref. 2 and
Ref. 3), a correction factor
γ is added to improve the approximation of the failure surface of concrete in multiaxial compression.
(3-77)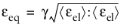
It is also possible to apply a User defined expression for defining the equivalent strain as a function of undamaged stress, stress components or strains.
(3-78)
,
Here, ε0 denotes the onset of damage, computed from the tensile strength
σts and Young’s modulus
E, so that
ε0 = σts/E. The parameter
εf is derived from other material parameters such as the tensile strength, the characteristic element size
hcb and the fracture energy per unit area
Gf, or the fracture energy per unit volume
gf.
(3-79)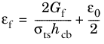
The Exponential strain softening law defines the damage evolution from
(3-80)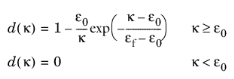
(3-81)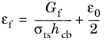
The Polynomial strain softening law defines the damage evolutions from
(3-82)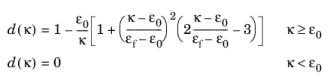
with εf according to
Equation 3-79.
The Multilinear strain softening law defines the damage evolutions from
(3-83)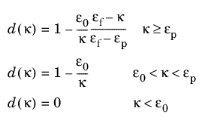
with εf according to
Equation 3-79 and
(3-84)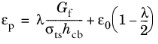
where λ is an input parameter that defines the shape of the curve.
The Mazars damage for concrete utilizes two different damage evolution laws, one for tensile damage and another for compressive damage. These two damage functions are combined as
(3-85)
here, αt and
αc are weight functions depending on the current stress state, and
β is the so-called
shear exponent, which determines the response in shear, that is, the evolution of the combined damage function in states where both damage functions are active.
To define the tensile damage evolution law dt(κ) (
Ref. 3), it is possible to use either
Linear strain softening,
Exponential strain softening, described in
Damage Evolution section; or
Mazars damage evolution function. A tensile
Mazars damage evolution function is obtained by a combination of linear and exponential strain softening
(3-86)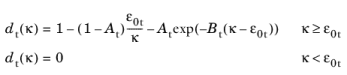
Here, At and
Bt are tensile damage evolution parameters, and
ε0t is the tensile strain threshold.
The compressive Mazars damage evolution function dc(κ) is obtained by
(3-87)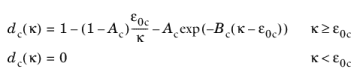
Here, Ac and
Bc are compressive damage evolution parameters, and
ε0c is the compressive strain threshold. Both the tensile and compressive damage evolution laws can also be specified by
User defined expressions.
This simplest regularization technique is based on stress-strain curves (damage evolution laws) that depend on the mesh and element characteristics. The method is often called the Crack Band method (
Ref. 4,
Ref. 5). The method regularizes the solution from a global viewpoint, which dissipates the correct amount of energy during strain localization. The main difficulty when using the crack band method is to find the correct width of the crack band,
hcb; which can depend on the element size and shape, as well as the order of the interpolation and the current stress state (that is, the inclination of the crack with respect to the mesh).
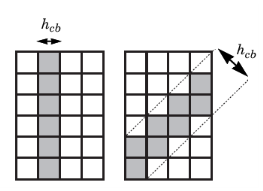
The crack band width hcb is then used to modify the
Damage Evolution law in which the damage variable
d(κ) is computed. Note that the damage evolution laws (
Equation 3-86 and
Equation 3-87) are unaffected by the crack band method.
The Implicit Gradient method (
Ref. 6) enforces a predefined width of the damage zone through a localization limiter. This is achieved by adding a nonlocal strain variable, the
nonlocal equivalent strain εnl, through an additional PDE where the equivalent strain
εeq acts as source term. This PDE is solved simultaneously with the displacement field:
(3-88)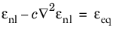
Here, the parameter c controls the width of the localization band. This parameter is defined from the internal length scale,
lint, and the geometry dimension
n (two or three dimension)
(3-89)
The strain-based formulation for the damage model (Equation 3-70) is then redefined by the nonlocal equivalent strain
εnl instead of the equivalent strain
εeq
(3-90)
A rate dependency can be introduced to the damage model by using the Delayed damage viscous regularization method available for time-dependent studies. The method can be used to model a real rate-dependent fracture problem, as well as for stabilizing a rate-independent problem. In both cases, a viscous damage variable
dv is introduced. This variable is defined through the following ODE
(3-91)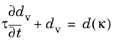
where τ is the characteristic relaxation time. For the case when the viscous regularization is used to stabilize a rate-independent fracture problem,
τ should be significantly smaller than the time step used by the solver in order not to modify the properties of the problem too much. The viscous damage variable
dv is then used in
Equation 3-69 to define the damaged stress tensor.
The Phase field damage model is closely related to the
Strain-based Damage Models, but it is derived from a different starting point. Following a similar derivation as reported in
Ref. 7, the model is based on the regularization of a variational formulation of the classical theory by Griffith for brittle fracture; where the geometric crack discontinuity is regularized by a second-order phase field. Including a viscous regularization of the crack phase field
ϕ, the energy functional governing the crack propagation takes the following form:
(3-92)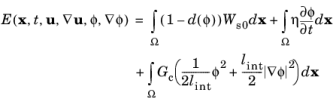
where d(ϕ) is the damage function,
Ws0 is the elastic strain energy density,
η is the viscosity,
Gc is the critical energy release rate, and
lint is the internal length scale that appears form the regularization of the discrete fracture.
Given the two dependent variables, u and
ϕ, the main contributions to the coupled initial boundary value problem (including inertial terms), are:
(3-93)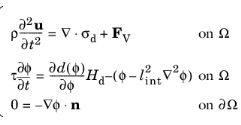
where the characteristic time τ and the state variable
Hd have been introduced. The state variable
Hd is a function of the crack driving force
Dd, and it satisfies the Kuhn–Tucker conditions so that:
(3-94)
The momentum balance in Equation 3-93 is included for completeness but is not implemented directly as part of the phase field damage model. However, the equation gives an indication that the damaged stress, as defined by
Equation 3-69, is used for the mechanical equilibrium.
The crack driving force, Dd, can be either a function of the elastic strain energy density, or it can also include dissipation processes.
By selecting the Elastic strain energy density, the crack driving force is derived from
(3-95)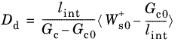
where Ws0+ is the tensile part of the undamaged elastic strain energy density. The strain energy threshold
Gc0 is an ad hoc variable introduced to establish an elastic threshold before damage occurs. By setting
Gc0 equal to zero recovers the model reported in
Ref. 7.
By selecting Total strain energy density, additional contributions from dissipative material features, such as creep, plasticity, and viscoelasticity, are added. Select the
Calculate energy dissipation check box in the parent material model to compute these variables.
(3-96)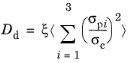
where σc is the
critical fracture stress,
σpi are the
undamaged principal stresses, and
ξ is a dimensionless parameter which determines the post peak slope.
It is also possible to enter a User defined expression for the crack driving force
Dd.
The damage variable d is in the phase field damage model a function of the crack phase field
ϕ. By selecting
Power law, the damage evolution function is defined as
(3-97)
where the exponent m is a user input. Often a quadratic function is used so that
m = 2. An alternative damage function was suggested in
Ref. 10. By selecting
Cubic, Borden, the damage evolution function
d(ϕ) reads
(3-98)
where the model parameter s controls the shape of the damage evolution function. The
Cubic, Borden option is only available when the crack driving force is defined through the strain energy density.
It is also possible to enter a User defined expression for the damage evolution
d as a function of the phase field variable
ϕ.
Typically, phase field damage models use a decomposition of the undamaged strain energy density Ws0 into a tensile and compressive parts. Only the tensile part
Ws0+ affects the phase field, and consequently the damage growth and fracture. Several alternative definitions of
Ws0+ are available in COMSOL Multiphysics.
The simplest alternative is to set Ws0+ equal to the complete strain energy density
Ws0, which means that no split is made into tensile and compressive counterparts. Select
No split in the
Exclude compressive energy list to achieve this. This option has the advantage that it greatly simplifies the structure of the equations, although that comes at the cost of physical correctness, especially for shear and cyclic loading.
A more accurate method is to use the volumetric-deviatoric split by selecting Volumetric only in the
Exclude compressive energy list. Here, only the positive part of the volumetric stress is considered while the entire undamaged deviatoric stress
σdev = dev(
σun) is included in
Ws0+. The definition of
Ws0+ then reads
(3-99)
where I1 = trace(
σun) is the first invariant of the undamaged stress tensor defined in
Equation 3-68 (see
Invariants of the Stress Tensor); and
εel,vol and
εel,dev are the volumetric and deviatoric parts of the elastic strain tensor, respectively (see
Invariants of Strain). For hyperelastic materials,
Equation 3-99 is replaced by
where Wiso is the isochoric strain energy density,
Wvol is the volumetric strain energy density, and
Jel is the elastic volume ratio. The split is only available if the parent hyperelastic model permits a clear split of
Ws into two parts.
Another alternative is to define Ws0+ by performing a spectral decomposition of the stress tensor such that
(3-100)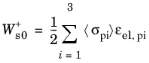
where σpi are the principal values of the undamaged stress tensor
σun, and
εel,pi are the principal values of the elastic strain tensor
εel (see
Principal Strains).
(3-101)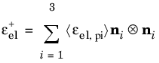
(3-102)
(3-103)
Both the Spectral decomposition, stress and
Spectral decomposition, strain options involve computing the principal values and principal vectors. Such operations are comparatively expensive and typically increase the computational cost of the phase field damage method, however, these are the most physically correct formulations to use.