The relation between stress amplitude, σa, and life,
N, is one of the oldest methods for fatigue evaluation. It is a very popular method since the relation can be easily obtained from fatigue tests. The relation takes two characteristic shapes, shown in
Figure 3-8. The upper shape, which decreases until a point where it becomes a horizontal line, represents materials that have an endurance limit. If the load amplitude in a load cycle is below the endurance limit, the component does not fail in fatigue. If the endurance limit is exceeded, the component does fail in fatigue if the number of load cycles is large enough. The number of cycles where the S–N curve becomes horizontal varies for different materials but is usually in the range of 10
6 to 10
8 cycles. Several materials do not have an endurance limit and experience fatigue even at low stress amplitudes. This fatigue behavior is demonstrated by the dashed line in
Figure 3-8.
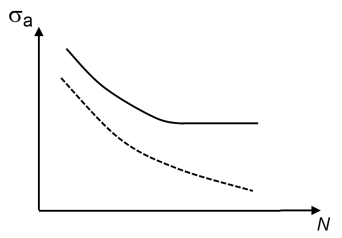
where Δσ is the stress range evaluated as the difference between the largest and the smallest stresses experienced during a fatigue cycle.
where σ1 is the largest principal stress,
σ3 is the smallest principal stress,
σvM is the equivalent stress according to von Mises, and
σh is the hydrostatic (or mean) stress.
where fSN denotes the S–N function. At low stresses the fatigue life is limited by a
Cycle Cutoff. At high stresses, when the stress amplitude exceeds the highest stress as defined by the S–N curve, the fatigue life cannot be determined. No results are computed in such regions. This is demonstrated in
Figure 3-9.

where σf and
b are material constants and
σa is the stress amplitude.
Nf is the number of load cycles to failure, and
2Nf is the number of load reversals. This relation becomes a linear in a log-log diagram and is often utilized in engineering applications. At low stresses the fatigue life is limited by a
Cycle Cutoff.
The transition stress between LCF and HCF is denoted by St, the transition life is denoted by
Nt, and the endurance limit or the endurance stress is denoted by
Se. The point that defines a knee on the S–N curve is denoted
Ne and is called the endurance life. Often the key parameters of the approximate curve are expressed using the ultimate tensile stress,
Su. In steel, for example, the values are roughly
St = 0.9
⋅ Su,
Nt = 10
3 cycles, and
Se = 0.5
⋅ Su,
Ne = 10
6 cycles.