Figure 2-7 shows the uniform thickness doubly curved laminated shell having an orthogonal curvilinear coordinate system (

) and a total thickness (
d).
A typical stacking sequence of a composite laminate having n layers is shown in
Figure 2-8. The thickness of each layer (
dk), as well as the fiber direction in each layer (
θk) with respect to first principal direction (
ξ1) of the laminate are indicated. A counterclockwise rotation of the fiber direction with respect to the (
ζ) direction is considered as positive.
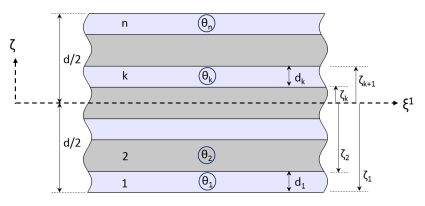
Sometimes, you want to write expressions that are functions of the coordinates in the thickness direction of the layered shell. If you write expressions based on the usual coordinates, like X,
Y, and
Z, such an expression will be evaluated on the reference surface (the meshed boundaries). In addition to this, you can access locations in the through-thickness direction by making explicit or implicit use of the coordinates in the extra dimension.
The extra dimension coordinate has a name like x_llmat1_xdim. The middle part of the coordinate name is derived from the tag of the layered material definition where it is created; in this example a
Layered Material Link.
Finally, the coordinates in 3D space are available using the physics scoped variables lshell.X,
lshell.Y, and
lshell.Z. These coordinates vary also in the thickness direction of the layered shell.
The default value for the through-thickness location is given in the Default through-thickness result location section of the Layered Shell interface.
The Layered Material dataset allows the display of results in 3D solid even though the equations are solved on a 2D surface.
Given only the homogenized stiffness and computed deformations, there is not enough information to compute stresses. The stress state will depend on the local geometry. In the Section Stiffness node, you have a possibility to define expressions for the relation between section forces and stresses. Such expressions must then be based on your knowledge of the peak stresses in the original, not homogenized structure. As an example, for a perforated structure, the stress concentrations around the holes should be taken into account.