The Embedded Reinforcement multiphysics coupling provides a generic method to couple lower dimension structural elements to a solid domain. Mesh elements from the Truss, Wire, Beam, or Membrane interfaces within or adjacent to a solid domain can be connected by adding this multiphysics coupling. Two different formulations are available for connecting the interfaces:
Rigid or
Spring connection. The rigid connection is based on a pointwise constraint formulation, while the spring connection is based on a penalty regularization of the constraint. When using the spring connection, a nonlinear behavior can be included by adding a bond slip model.
To facilitate the connection between the solid domain and the embedded structure, a nonlocal coupling is set up between the two interfaces. This coupling is made through a General Extrusion operator that maps an expression defined on the source to an expression that can be evaluated on the destination geometry. Here, the source is always the solid domain, and the destination is the embedded thin structure. The latter can be either a Truss, Wire, Beam, or Membrane interface. Mathematically, the mapping of a generic expression
E from a source domain
Ωsrc to a point
Xdst on the destination boundary (or edge)
Γdst can be described by
(3-219)
The mapping is such that for each point Xdst, it finds the closest point
Xsrc in
Ωsrc at which to evaluate
E. From
Equation 3-219 it is inferred that the mapping is made in the material frame, that is, the mapping is constant even for a geometrically nonlinear case. Moreover, the mapping is only valid for the part of
Γdst that lies within
Ωsrc.
With the definition in Equation 3-219, the rigid connection type is described by adding a constraint on
Γdst such that the displacement field
u equals
From the relative displacement vector Δu, the spring force
f of the penalty formulation is defined by Hooke’s law
where K is the spring stiffness matrix, which has nonzero components on the diagonal only. The spring stiffness matrix
K is most naturally described in the local coordinate system of the thin structure,
Γdst, such that the spring force
fl in local coordinates is defined by
where T is the transformation matrix form local to global coordinates and
Kl is the spring stiffness matrix in the local coordinate system. The local coordinate system is either defined by the destination physics interface, or automatically by the multiphysics coupling. Finally, the following weak contribution is added
When a Bond slip model is added to the spring connection, an additive decomposition of
Δu into elastic and plastic counterparts is assumed so that, in the local coordinate system
where ul,e is the elastic displacement, and
ul,p is the plastic displacement (or slip) on the destination. The definitions of the spring force and the weak contribution are unaffected.
The slip vector ul,p is defined through a local constitutive model based on the flow theory of plasticity. When the destination physics is either a Truss, Wire, or a Beam interface, slip can only occur in the direction of the local edge tangent, which means that the slip vector is defined by a single scalar value, that is,
ul,p = {0,0,upn}. The constitutive model is then summarized by
(3-220)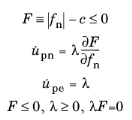
where fn and
upn is the spring force and slip in the direction of the local edge tangent, respectively. The cohesion
c determines the sliding resistance, and it can depend on any variable or field present in the model. The plasticity model is defined by the yield function
F, the plastic multiplier
λ, and the accumulated slip
upe. The last row of
Equation 3-220 are the Kuhn-Tucker conditions.
(3-221)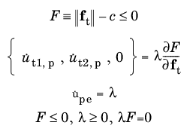
where ft is a vector containing the two tangent components of the local spring force
fl.
The rate equations in the constitutive models given by Equation 3-220 and
Equation 3-221 are implemented through a backward Euler discretization. The resulting set of nonlinear algebraic equations is solved using Newtons method to find
λ, upe, and
ul,p. Optionally, it is also possible to compute the dissipated energy due to friction,
Wp, by also solving the following rate equation
|
When the Embedded structure is a Beam interface, there is an option to suppress rotation around the beam axis. This option adds a constraint for the rotation θxl around the beam axis. The constraint is implemented using a penalty regularization, which adds the following weak contribution to the model
where GJ is the torsional stiffness of the beam and A is the area of the beam. This functionality is intended to suppress unwanted rigid body rotations that can lead to nonconvergence of the solver.
|