A prerequisite for setting up the mechanical contact problem is to define the contact search between the source boundary and the destination boundary. The purpose of the search is to detect points on the contacting boundaries that are in contact or may come in contact, and also to map quantities between such points. This part of the contact problem is defined in the Contact Pair that sets up relevant variables and operators to map quantities between the selected source and destination boundaries. In COMSOL Multiphysics, the contact search is made using a ray-tracing strategy as depicted in
Figure 3-39. For mechanical contact, most variables and equations are formulated on the destination boundary. Hence, the typical mapping of interest here is from the source boundary to the destination boundary, however, it is possible to map quantities in the opposite direction as well.
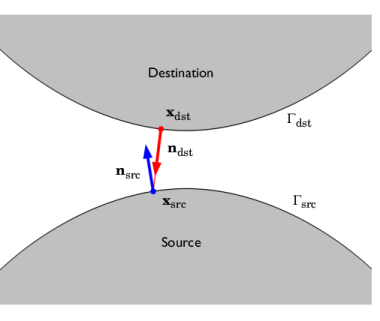
For each point xdst in the spatial frame on the destination boundary
Γdst, the closest point
xsrc in the spatial frame on the source boundary
Γsrc in the direction of the destination spatial normal
ndst is sought. Such a mapping can be described through an operator map
(E, x), where
E is some generic quantity or expression, and
x is the point to which
E is mapped. Using this mapping operator, the coordinates of the mapped point on
Γsrc is
where x is the spatial coordinates that parameterize
Γsrc. For brevity, the second argument of the mapping operator is omitted in the following and it should be understood that the mapping occurs to a point
xdst on
Γdst if nothing else is specified.
An important quantity for contact mechanics is the gap function ggeom(
x) defined as the geometric distance between the source and the destination boundary. Note that
ggeom(
x) is not necessarily the closest distance between the two boundaries. Using the mapping operator, the gap distance at
xdst is defined as
|
•
|
A Contact Pair sets up mapping operators that can be used in any expression to map quantities from the source to the destination boundary with the syntax src2dst_<pair_tag>(expr).
|
•
|
The mapping by default uses the spatial frame normal. If the Mapping method in the Contact Pair is changed to Initial configuration, the mapping is instead performed in the direction of the material frame normal. This means that the direction of the mapping is constant and not affected by how the contacting boundaries deform.
|
|
(3-192)
where doffset,s and
doffset,d is the offset from the source and destination boundary, respectively. Each offset variable can vary along the geometry, and may also vary in time (or by the parameter value when using the continuation solver). The correction of the source side offset is necessary since the normal of
xsrc,
nsrc =
map(
n), is not necessarily pointing toward
xdst as illustrated in
Figure 3-39. When the geometric surfaces are in contact, the normals will be exactly opposite such that
nsrc =
−ndst.
(3-193)
where X is the material coordinates, and
F is the deformation gradient that contains information about the local rotation and stretch. Note that the mapping is made between points in the spatial frame as clarified in the equation. Both quantities are mapped from the source to the destination boundary. Constitutive models for the mechanical problem are typically formulated on an incremental form. COMSOL Multiphysics applies a backward Euler approximation to
Equation 3-193 so that the incremental slip at
xdst is
where Xsrc,old is the mapped material coordinates at the previous increment.
When a Contact node is added to a Shell, Layered Shell, or Membrane interface, the material and spatial frames used in the contact mapping are adjusted to account for the thickness of the structural element by considering the physical position of its top and bottom surface relative to the geometric boundary. This also applies to boundaries that intersect the selection of a
Thin Layer node in the Solid Mechanics interface. For example, the contact material coordinates
Xcnt and the spatial coordinates
xcnt in a Contact node added in the Shell interface are defined as
where z is the offset from the geometric boundary to the considered contact boundary. The definition of the geometric gap is then accordingly adjusted and given as
where ndst is to be interpreted as the normal of the contact boundary. For the Shell interface, the direction of
ndst coincides with the normal of the geometric boundary, but so is not always the case. This applies to
nsrc as well. Note also the that mapping is made between the modified spatial coordinates. Similar corrections are also made for other quantities such as the incremental slip
Δgt where the
Xcnt is used instead of
X. The same concept is used for other cases where the contact boundary does not coincide with the geometric boundary, but the definition of
Xcnt and
xcnt may differ.