Loss coefficients, Ki, for turbulent flow are available in the literature (
Ref. 15) and the set predefined in the Pipe Flow interface is reproduced in the table below:
Above, β is the ratio of small to large cross-sectional area. The point friction losses listed above apply for Newtonian fluids. Point losses applying to non-Newtonian flow can be added as user-defined expressions, for instance from (
Ref. 16).
Several options to specify pressure drop across the T-junction branches are available. If the Loss coefficients option is selected, the energy loss between main branches and junction and the he energy loss between the side branch and junction are calculated as
The Loss coefficient with respect to common branch option, that is available for the Pipe Flow interface, implements the loss coefficients according to
Ref. 28. The pressure loss for T- junction is often expressed in terms of the flow in the common branch. For joining flows, the common branch is the collector branch (
Figure 2-2, left)
The Loss coefficients, extended model option, that is available for the Pipe Flow interface, allows you to specify the loss coefficient in more details and account for the flow directions. Enter values or expressions for the six dimensionless loss coefficients. See
Figure 2-2-
Figure 2-3.
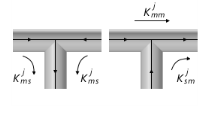
Use the Pressure drops option to specify a value or expression for the pressure drop explicitly for each branch respectively: