Non-Newtonian fluids are found in a great variety of processes in the polymer, food, pharmaceutical, cosmetics, household, and fine chemicals industries. Examples of these fluids are coatings, paints, yogurt, ketchup, colloidal suspensions, aqueous suspensions of drugs, lotions, creams, shampoo, suspensions of peptides and proteins, to mention a few. The Polymer Flow Module is an optional add-on package for COMSOL Multiphysics designed to aid engineers and scientists in simulating flows of non-Newtonian fluids with viscoelastic, thixotropic, shear thickening, or shear thinning properties. Simulations can be used to gain physical insight into the behavior of complex fluids, reduce prototyping costs, and to speed up development. The Polymer Flow Module allows users to quickly and accurately model single-phase flows, multiphase flows, nonisothermal flows, and reacting flows of Newtonian and non-Newtonian fluids.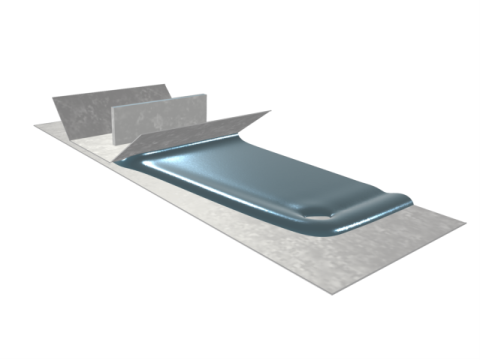
The Polymer Flow Module can solve stationary and time-dependent flows in two-dimensional and three-dimensional domains. Formulations suitable for different types of flow are set up as predefined Fluid Flow interfaces, referred to as physics interfaces. These Fluid Flow interfaces use physical quantities, such as velocity and pressure, and physical properties, such as density and viscosity, to define a fluid-flow problem. Different physics interfaces are available to cover a range of flows. Examples include: Laminar Flow, Creeping Flow, Viscoelastic Flow, Heat Transfer, and Transport of Diluted Species. The physics interfaces can be combined with the interfaces in the Mathematics branch (Level Set, Phase Field and Ternary Phase Field), or defined on an Arbitrary Lagrangian Eulerian (ALE) frame to simulate two- and three-phase flows, and rotating flows. The Polymer Flow Module includes a set of predefined multiphysics couplings, including: Nonisothermal Flow; Reacting Flow; Two-Phase Flow, Level Set; Two-Phase Flow, Phase Field; Three-Phase Flow, Phase Field; and Rotating Machinery, Fluid Flow, to facilitate the setup of multiphysics simulations.