Several distinct regions typically exist in a DC discharge, depending on the specific operating conditions and geometry. A typically DC discharge is shown below. The cathode glow (often known as cathode fall) region is where most of the voltage drop occurs. This is the region where the discharge current is built up due to the high degree of ionization. The electron density and flux grow exponentially in this region (
Ref. 5). The negative glow and Faraday space regions connect the cathode glow to the positive column. In this region the electron temperature drops rapidly due to the fact that the electric field is very weak. In the positive column region, the discharge is very uniform, and the electron-ion pairs generated are lost to the walls in the radial direction due to the ambipolar field (
Ref. 5).
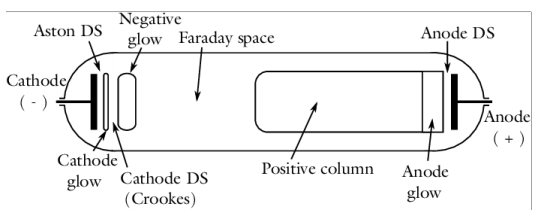
Inductively coupled plasmas (ICP) were first used in the 1960s as thermal plasmas in coating equipment, Ref. 4. These devices operated at pressures on the order of 0.1 atm and produced gas temperatures on the order of 10,000 K. In the 1990s, ICP became popular in the film processing industry as a way of fabricating large semiconductor wafers. These plasmas operated in the low-pressure regime, from 0.002–1 Torr and, as a consequence the gas temperature remained close to room temperature. Low-pressure ICP are attractive because they provide a relatively uniform plasma density over a large volume. The plasma density is also high, around 10
18 1/m
3, which results in a significant ion flux to the surface of the wafer. Faraday shields are often added to reduce the effect of capacitive coupling between the plasma and the driving coil. This reduces the effect of ion bombardment on the dielectric window, which can lead to degradation and contamination of the chamber. Some typical ICP configurations are shown in the figure below.
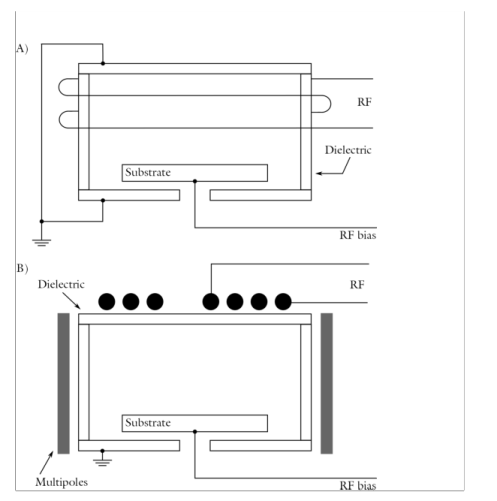
Typical operating conditions for capacitively coupled plasmas are driving voltages from 100–1000 V, pressures of 2–200 Pa, electron densities in the region of 1015–10
17 1/m
3 and electron temperatures on the order of 2–20 eV. The operating frequency is typically 13.56 MHz, which is one of the frequencies reserved worldwide for the industrial, scientific, and medical uses.
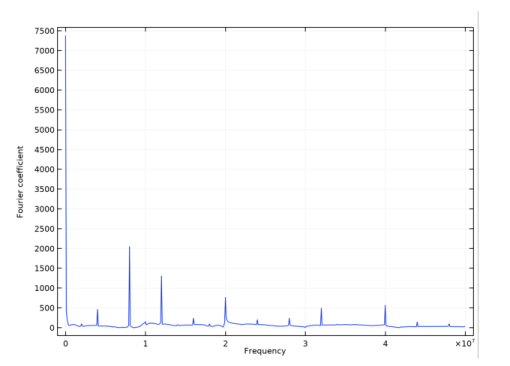
Microwave plasmas, or wave heated discharges, are sustained when electrons can gain enough energy from an electromagnetic wave as it penetrates into the plasma. The physics of a microwave plasma is quite different depending on whether the TE mode (out-of-plane electric field) or the TM mode (in-plane electric field) is propagating. In the 2D axisymmetric case, the TE mode means that only the azimuthal component of the electric field is computed and the TM mode means that the in-plane,
r and
z components of the electric field are computed. In both cases it is not possible for the electromagnetic wave to penetrate into regions of the plasma where the electron density exceeds the critical electron density (around 7.6x10
16 1/m
3 for argon at 2.45 GHz). On this contour corresponding to the critical electron density, the wave goes from being propagating to evanescent. This means that all the power from the wave is absorbed in a very small region in space, which can make the model numerically unstable. The pressure range for microwave plasmas is very broad. For electron cyclotron resonance (ECR) plasmas, the pressure can be on the order of 1 Pa or less. For non-ECR plasmas the pressure typically ranges from 100 Pa up to atmospheric pressure. The power can range from a few watts all the way up to several kilowatts. Microwave plasmas are popular due to the cheap availability of microwave power.
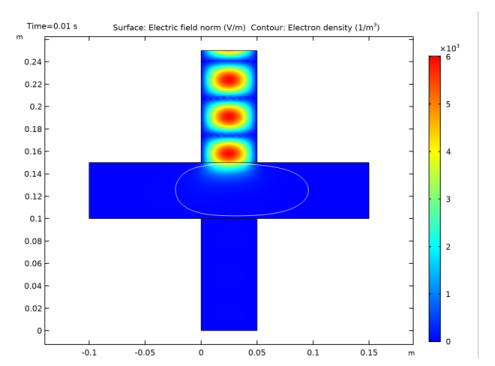