Using the Chain Drive node in the Multibody Dynamics interface, you can model a roller chain sprocket assembly in 2D or 3D. The Chain Drive node determines the interaction of the chain drive assembly, and automatically generates a set of physics nodes that are used to describe its behavior.
This is a domain selection input used to create a Rigid Domain node on each link plate of the chain. If you use a geometry from the COMSOL Part Library, a built-in domain selection named Links is automatically selected. If you are using your own geometry, you need to input a domain selection containing all link plates. This selection input is available only when the chain links are modeled as rigid bodies.
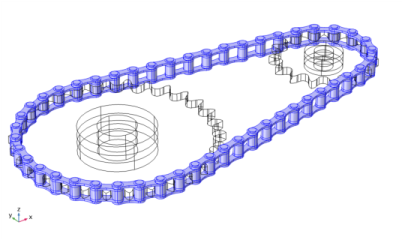
This is a domain selection input used to create a Rigid Domain node on each sprocket. If you use a geometry from the COMSOL Part Library, a built-in domain selection named Sprockets is automatically selected. If you are using your own geometry, you need to input a domain selection containing both sprockets domains. This selection input is available only when the sprockets are modeled as rigid bodies.
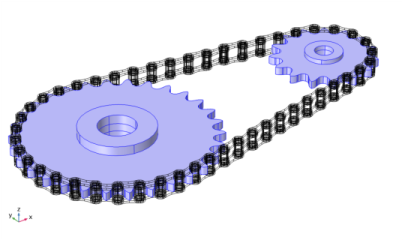
For 2D models created from the COMSOL Part Library, a selection named Pin Inner Boundaries is automatically selected. If you use your own geometry, you need to input a boundary selection containing the inner boundaries of all pin plates.