The theory of laminated shells is discussed in this section. The Layered Linear Elastic Material node in the Shell interface allows the modeling of laminated shells, also popularly known as composite laminates, having different orthotropic properties per layer. The first order shear deformation theory (FSDT) is used to find homogenized equivalent material properties of a composite laminate.
Figure 5-3 shows a doubly curved laminated shell with uniform total thickness,
d. It is represented by orthogonal curvilinear coordinate system (

). The geometry representation of a layered shell is same as a single layer shell as discussed in the
Geometry and Deformation section.
A typical stacking sequence of a composite laminate having n layers is shown in
Figure 5-4. The thickness of each layer (

), as well as the fiber direction in each layer (

) with respect to first principal direction (

) of the laminate are indicated. An anticlockwise rotation of the fiber direction with respect to (

) direction is considered as positive.
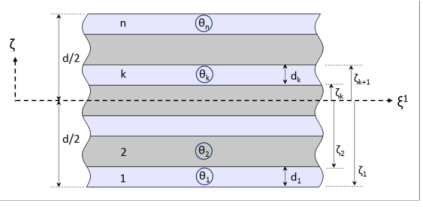
For n number of layers in a laminate, there are
n+2 variables (unknowns) and thus
n+2 equations are needed to solve them. The first
n+
1 equations are the form of shear stress continuity can be written as:
The default value of though thickness location is given in the Default through-thickness result location section of the Layered Shell interface.
The Layered Material data set allows the display of results in 3D solid even though the equations are solved on a 2D surface.