In the augmented Lagrangian method, the system of equations is solved in a segregated way. Augmentation components are introduced for the contact pressure Tn and the components
Tti of the friction traction vector
Tt. An additional iteration level is added where the usual displacement variables are solved separated from the contact pressure and traction variables. The algorithm repeats this procedure until it fulfills a convergence criterion.
In the following equations F is the deformation gradient matrix. When looking at expressions evaluated on the destination boundaries, the expression
map (E) denotes the value of the expression
E evaluated at a corresponding source point, and
g is the current gap distance between the destination and source boundary.
Both the contact map operator map (E) and the gap distance variable are defined by the contact element
elcontact. For each destination point where the operator or gap is evaluated, a corresponding source point is sought by searching in the direction normal to the destination boundary.
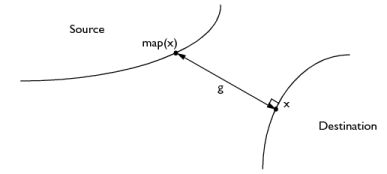
It is possible to add an offset value both to the source (osrc), and to the destination (
odst). If an offset is used, the gap will be computed with the geometry treated as larger (or smaller, in the case of a negative offset) than what is actually modeled. The offset is given in a direction normal to the boundary. It can vary along the geometry, and may also vary in time (or by parameter value when using the continuation solver).
The effective gap distance dg used in the analysis is thus
and Xm,old is the value of
Xm in the last converged time or parameter step. The coordinates are material (undeformed) coordinates. The slip vector is thus approximated using a backward Euler step. The deformation gradient
F contains information about the local rotation and stretching.
Using the special gap distance variable (solid.gap), the penalized contact pressure
Tnp is defined on the destination boundary as
pn is the user-defined normal penalty factor.
The penalized friction traction Ttp is defined on the destination boundary as:
In Equation 3-57,
pt is the user-defined friction traction penalty factor. The critical sliding resistance,
Tt,crit, is defined as
In Equation 3-58,
μ is the friction coefficient,
Tcohe is the user-defined cohesion sliding resistance, and
Tt,max is the user-defined maximum friction traction.
In the following equation δ is the variation (represented by the
test() operator in COMSOL Multiphysics). The contact interaction gives the following contribution to the virtual work on the destination boundary:
where wcn and
wct are contact help variables defined as:
where i is the augmented solver iteration number and
γfric is a Boolean variable stating if the parts are in contact or not.
where dg is the effective gap distance,
pn is the penalty factor, and
p0 is the pressure at zero gap. The latter parameter can be used to reduce the overclosure between the contacting boundaries if an estimate to the contact pressure is known. In the default case, when
p0 = 0, there must always be some overclosure (a negative gap) in order for a contact pressure to develop.
This can be viewed as a tangential spring giving a force proportional to the sliding distance. The penalty factor pt can be identified as the spring constant. The sticking condition is thus replaced by a stiff spring, so that there is a small relative movement even if the force required for sliding is not exceeded.
The definition of Tt,crit depends on the algorithm used for computing the normal contact.
where μs is the static frictional coefficient,
μd is the dynamic frictional coefficient,
vs is the slip velocity, and
αdcf is a decay coefficient.
You can model a situation where two boundaries stick together once the get into contact by adding an Adhesion subnode to
Contact. Adhesion can be modeled when the penalty contact method is used. The adhesion formulation can be viewed as if a thin elastic layer is placed between the source and destination boundaries when adhesion is activated.
When adhesion is active, the tensile stress σn in the normal direction is computed from the effective gap
dg as
The default value for the stiffness in the normal direction Kp is the penalty stiffness of the contact condition, but you can also enter it explicitly. In compression, the penalty stiffness is always used. This leads to a bilinear stiffness in the normal direction when
Normal stiffness is
User Defined.
where
is a coefficient with the default value 0.17. This coefficient can either be input explicitly, or be computed from a Poisson’s ratio. A plane strain assumption is used for this conversion, giving
As a measure of the displacement in the adhesive layer, the mixed mode relative displacement um, is defined as weighted combination of the normal direction displacement
uI and the tangential displacement
uII.
The failure initiation displacement ui0 for each mode is determined from the maximum stress and the elastic stiffness, as
The decohesion displacement uif for each mode is implicitly determined from the given energy release rate (which is the area under the stress vs. displacement curve):
The final mixed mode failure displacement depends on the selected Failure criterion. The
Power Law failure criterion is defined as
whereas the Benzeggagh-Kenane failure criterion is defined as
All expressions presented under Linear separation law are still valid except the damage function, which now is
This law requires one more material parameter λ, describing the width of the “plastic” region. The
Shape factor λ is the ratio between the plastic (constant stress) part of
Gic and the total “inelastic” part of
Gic: